Plasma cutters SHP 130A, 260A, 460A
The SHP plasma cutter is a modern and innovative device based on the construction of the gate. The portal is made of a light, yet stiffened profile, which guarantees high dynamics and precision of the cutting process.
AC servo motors are responsible for machine drive in all four axes. The latest achievements in the field of computer science have allowed us to adjust a proven and stable controller to the highest customer requirements. The modular design allows you to add all available machine options at any time without prior special machine preparation.
All machines offered and sold in Poland are standard equipped with a plasma source in HD technology (Narrow-stream plasma) and an automatic gas console that selects the cutting parameters to the desired technology and makes the production process of the companies much easier and faster.
AJANCNC 952® Control
based on an industrial computer powered by P3 processor 1.2 GHZ CPU provides fast control response and very low failure rate. It has many necessary functions needed for efficient work operators.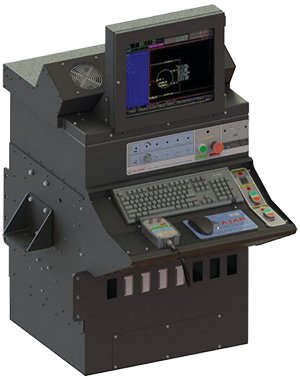
AJANCNC 952® Control
The biggest advantages of this system are:
- energy-resistant system,
- over 40 basic geometric forms called "MAKROS",
- AJANCAD installed on the controller,
- ability to build drawings on the machine,
- option to set sheet curvature (automatic),
- multiple positioning of the burner after a power failure,
- database of plasma and oxygen cutting parameters,
- the possibility of interfering with the cutting process using a hand held remote control,
- data transmission via USB, network and Wi-Fi,
- ability to cut a drawing directly from DXF.
Plasma torch
Plasma torches SCT 130® / SCT 260® / SCT 260B® were implemented in 2009. This model allows more efficient use of gas. It is cooled by a special liquid, thanks to which (with proper circulation) it extends the life and service life of consumables to a large extent.
As a standard it is equipped with a capacitive distance sensor built into the body of the burner, as well as a plasma arc voltage measurement sensor. The type of SCT burner has been prepared for cooperation with the automatic gas console EAK 130® , and the anti-collision sensor protects it's against mechanical damage.
Height measurement of sheet
AJAN cutters allow you to choose the type of sheet height measurement. Depending on the type of sheet metal you are using (thickness and type), the operator can choose arc, touch and capacitive measurements. This option is active only during the puncturing process. In the cutting cycle, the controller always automatically switches the measurement to the arc.
Arc measurement
it is used for thin materials, where the touch measurement can cause material displacement, while capacitive because of the rust it misread its values.
Capacitive measurement
the oldest method of testing the height of the sheet, however it fails on dirty sheets and when measuring height at the edge.
Touch measurement
It is used for thicker and rusty sheets.
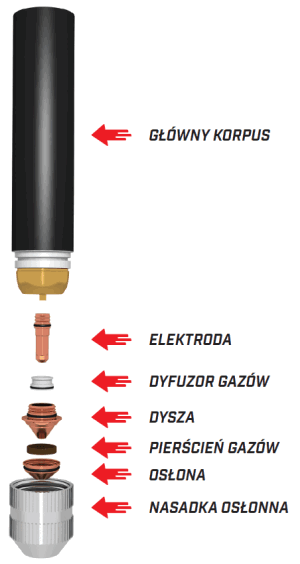
Palnik plazmowy
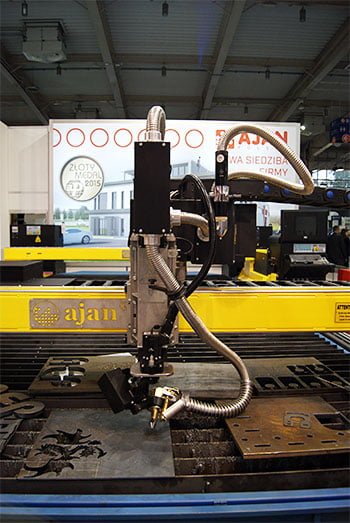
Support z palnikiem plazmowym i głowicą 3D tlenowo-gazową
PerfectHole® technology
A technology developed by AJAN technologists, based on improved firing of openings. When using the above mentioned technology, the sheet thickness factor to the minimum diameter is currently 1: 1 (from 6 mm to 20 mm). An important facilitation is the lack of operator intervention during the device programming process.
However, remember that "PerfectHole®" has been developed exclusively for black steel and up to a maximum thickness of 20 mm (SHP260®).
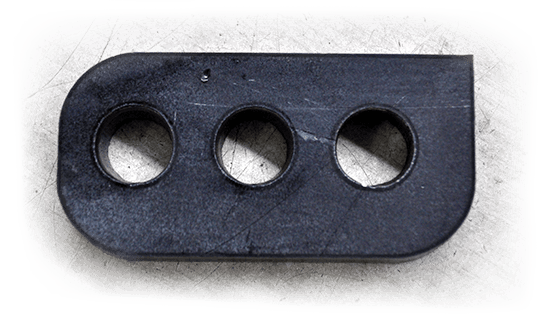
Technologia PerfectHole
Function AUTO - Z
The function available for AJAN cutters consists in finding the zero point by the machine as well as setting the curvature of the sheet. It is enough to press a button and the machine will automatically perform the positioning with very high accuracy in a few seconds. It consists in the fact that the cutter uses the moplasm to determine the lines in the X and Y axes of the machine, which end at the edges of the sheet, recalculates them and thus finds the zero point and determines the curvature of the sheet.
Advantages of the AUTO - Z function
- the operator is able to prepare a smoking sheet very quickly and accurately,
- the waste of baked metal is reduced to a minimum,
- we will also use this function when burning with the chamfering head details for welding so-called technological phases X, Y, K.
Microjoint function
Is only available in AJAN plasma cutters. This feature has been used for a long time now in sawing machines laser
This works on the principle of a temporary, smooth reduction of current during cutting in order to burn the workpiece. It is important that during this function the plasma arc is not extinguished and re-ignited (there are no more punctures and wear of the parts), while the detail is unburnt only on a small sheet thickness, eg when the 5 mm sheet is burned, less than 1 mm thick will be burnt underneath. Thanks to this very easily break such a detail from the sheet metal.
This function can be used in many cases. Clients very often include it when firing belts where due to thermal effects immediately after firing they would be wavy.
Thanks to the described function, this is not the case, and breaking them is not a major problem. The same is true for the burning of small details. To to prevent them falling into the table, activate (with one button) MICROJOINT, which prevents these problems.
IMPORTANT: a feature available as standard in plasma cutters.
System taking into account cathode and electrode consumption
This option only exists on AJAN® systems. The electrode installed in the burner is worn during break. This is synonymous with a voltage drop of up to 20V. This drop is used to measure the cutting height. For example, a burner set at a height of 3mm is able to get up to 1000 punches.
During the THC OTO® function, the differential arc for each burn has a reference point that is located in the center of the nozzle. The difference in voltage is transformed in the CNC controller and automatically corrects the position of the burner.
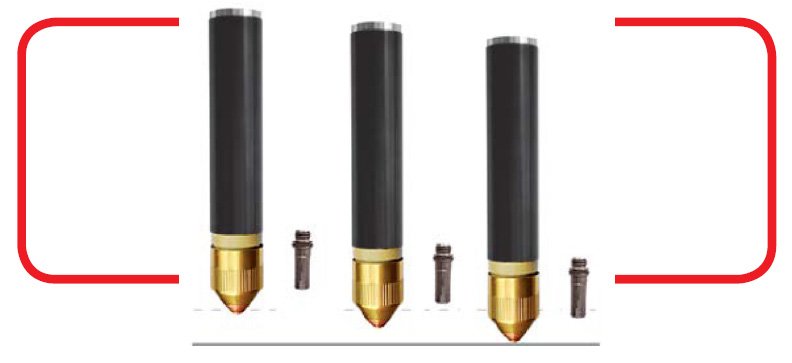
Conventional system
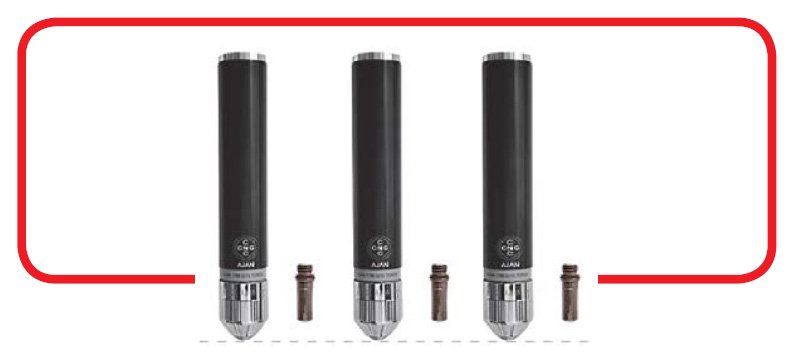
THC OTO® Supervisory System
Line and point routing
Plasma cutters with an HD source [SHP 130®, SHP 260® and SHP 460®] as standard have a line and point routing module. They enable gouging with a specific one depth in the indicated places on the baking tray. As an example of using this option, you can specify bending or welding lines or detailing lines for linear routing, and drill points for point routing. Fast technology change cutting routing and vice versa is possible with the automatic EAK 130® gas console placed on a plasma cutter. This process takes place automatically without operator interference as well machine downtime.
Extraction table
AJAN® has prepared a ventilation system and filtration allowing extraction and neutralization harmful dust and fumes (even those invisible) emerging during the plasma cutting process. It consists mainly of a ventilation unit, filter and extraction table.
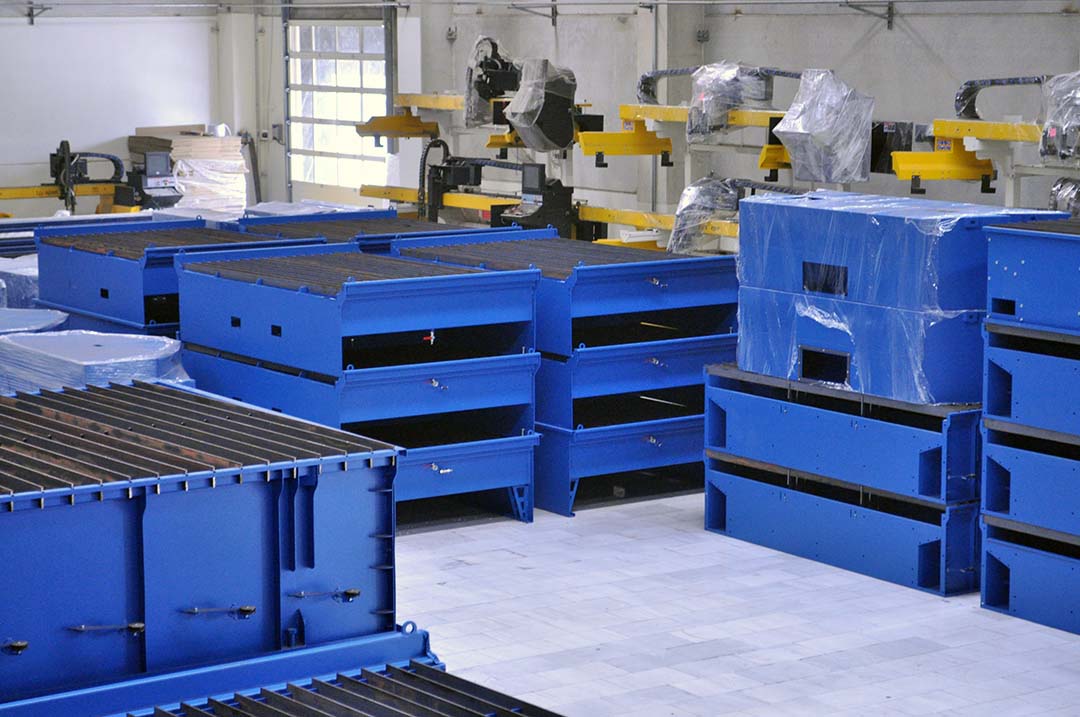
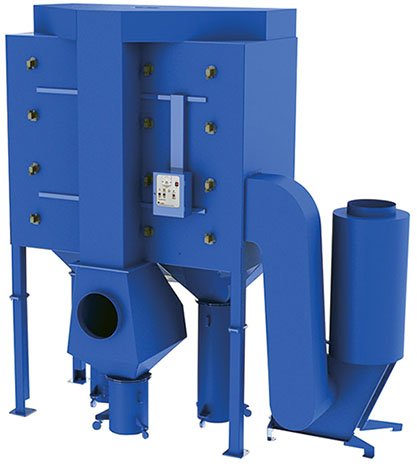
Ventilation
The filtering system is produced comes in 3 different sizes and selected for the machine depending on the dimensions work table, number of portals and sources. The whole unit is controlled by electronic filter purifier. Each the system is equipped with protection against fiery. Protective system it is constructed in such a way that he picked up all the particles he had ignited, cigarette butts, etc.
Advantages of extraction tables:
- Is divided into sections every 500 mm, where each of them is activated during drive the cutter over the section.
- In the extraction table, the flaps are opened and closed mechanically. This is a big advantage of our construction, thanks to which the mechanism of opening the dampers is more durable, cheaper and easier in operation. It is not exposed to overheating or pollution.
- Option to extend at any time.
- Optional strengthened or water table.
- Easy to exchange grids on their own and bathtubs for cleaning from waste.
Q m3 / h | Filter type AJF | m2 |
---|---|---|
6000 | 8 | 192 |
8000 | 12 | 288 |
10000 | 16 | 384 |